فرآوری آهن: سفری از دل سنگ تا اوج صنعت
فرآوری آهن، سفری شگفتانگیز و پیچیده است که از دل سنگهای بیجان، فلز ارزشمند آهن را استخراج میکند و به قلب صنعت و تمدن هدیه میدهد. این فرآیند، شاهدی بر خلاقیت و نوآوری بشر در مسیر رام کردن طبیعت و خلق دستاوردهایی حیرتانگیز است. در این مقاله، با مراحل شگفتانگیز فرآوری سنگ آهن، روشهای نوین و سنتی آن و نقش بیبدیل آهن در صنایع مختلف آشنا خواهیم شد.
در دنیای امروز، فولاد به عنوان آلیاژی از آهن، ستون فقرات بسیاری از سازهها و ماشینآلات را تشکیل میدهد. از آسمانخراشهای سر به فلک کشیده تا اتومبیلهای مدرن و ظریف، ردپای آهن در تار و پود زندگی انسان هویداست. فرآوری آهن، کلید دستیابی به این فلز ارزشمند و حیاتی است.
در این مقاله، با زبانی ساده و شیوا به مفاهیم کلیدی فرآوری سنگ آهن، مراحل مختلف این فرآیند و کاربردهای بیشماری که آهن در صنایع مختلف دارد میپردازیم.
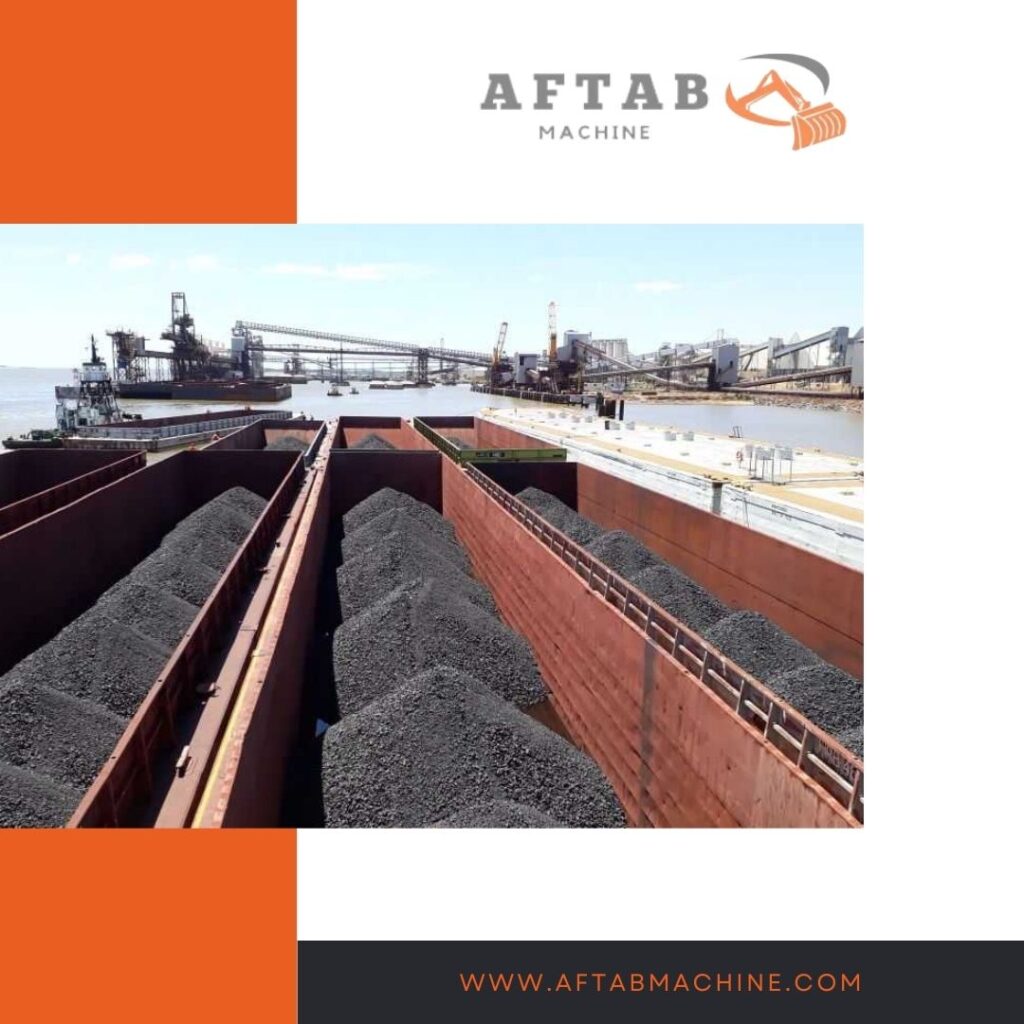
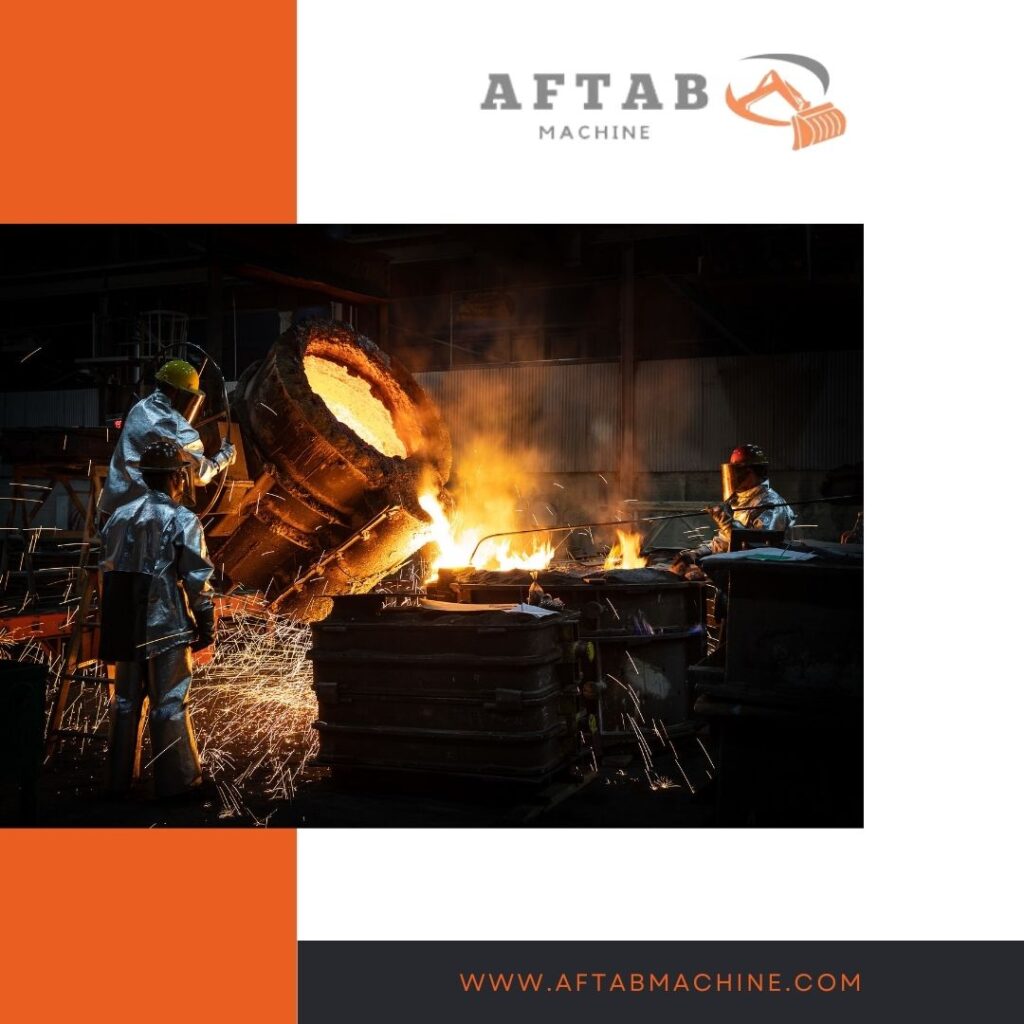
فرآوری آهن چیست؟
فرآوری آهن، فرآیندی چند مرحلهای و پیچیده است که طی آن، سنگ آهن با عیار پایین، به فلز آهن خالص و قابل استفاده تبدیل میشود. این فرآیند شامل مراحل مختلفی از جمله استخراج سنگ آهن، خرد کردن و آسیاب آن، جداسازی ناخالصیها و احیای سنگ آهن به فلز آهن میشود.
در طبیعت، سنگ آهن به صورت مخلوط با کانیهای دیگر یافت میشود. هدف از فرآوری سنگ آهن، جداسازی این فلز ارزشمند از ناخالصیها و افزایش عیار آن است. فرآیند فرآوری سنگ آهن، نقشی کلیدی در تولید فولاد ایفا میکند که به عنوان یکی از مهمترین آلیاژهای فلزی در صنایع مختلف از جمله ساختمانسازی، خودروسازی، لوازم خانگی و صنایع سنگین مورد استفاده قرار میگیرد.
مراحل فرآوری سنگ آهن به نوع سنگ آهن، ناخالصیهای موجود در آن و تکنولوژیهای مورد استفاده در کارخانههای فرآوری بستگی دارد. با این حال، به طور کلی میتوان این فرآیند را به مراحل خردایش و آسیاب، غنیسازی، پیشگرمایش و احیا تقسیم کرد.
در مرحله خردایش و آسیاب، سنگ آهن به قطعات کوچکتر تبدیل میشود. سپس، در مرحله غنیسازی، از روشهای مختلفی مانند جداسازی مغناطیسی، ثقلی یا flotation برای جداسازی کانیهای آهن از ناخالصیها استفاده میشود. در مرحله پیشگرمایش، سنگ آهن غنی شده تا دمای بالایی گرم میشود و در نهایت، در مرحله احیا، اکسیژن از سنگ آهن جدا شده و فلز آهن خالص به دست میآید.
فرآوری آهن، فرآیندی ضروری و حیاتی برای تولید فولاد و توسعه صنایع مختلف است. با درک عمیق این فرآیند و مراحل مختلف آن، میتوان به نقش بیبدیل آن در دنیای مدرن و زندگی انسان پی برد.
جزئیات کامل درباره خط خردایش سیار را اینجا بخوانید.
روش های فرآوری آهن
فرآوری سنگ آهن، مسیری متنوع با روشهای مختلف است که هر کدام مزایا و معایب خاص خود را دارند. انتخاب روش مناسب فرآوری، به عواملی مانند نوع سنگ آهن، ناخالصیهای موجود در آن، ظرفیت کارخانه فرآوری و مسائل اقتصادی بستگی دارد. در ادامه، به معرفی برخی از روشهای متداول فرآوری آهن میپردازیم:
- روشهای مغناطیسی: این روش از خاصیت مغناطیسی برخی از کانیهای آهن مانند مگنتیت برای جداسازی آنها از ناخالصیها استفاده میکند. در این روش، سنگ آهن خرد شده از میان یک میدان مغناطیسی عبور داده میشود و کانیهای آهن به دلیل خاصیت مغناطیسی خود جذب شده و از ناخالصیها جدا میشوند.
- روشهای ثقلی: در این روش، از تفاوت وزن مخصوص کانیهای آهن و ناخالصیها برای جداسازی آنها استفاده میشود. سنگ آهن خرد شده در مخلوطی از آب و مواد شیمیایی ریخته میشود و ذرات با وزن مخصوص بیشتر (کانیهای آهن) در ته مخزن ته نشین شده و ذرات با وزن مخصوص کمتر (ناخالصیها) در بالای مخزن شناور میشوند.
- روشهای flotation: این روش از حبابهای هوا برای جداسازی کانیهای آهن از ناخالصیها استفاده میکند. در این روش، سنگ آهن خرد شده در مخلوطی از آب و مواد شیمیایی ریخته میشود و حبابهای هوا به ذرات کانیهای آهن متصل شده و آنها را به سطح مخزن هدایت میکنند، در حالی که ناخالصیها در ته مخزن باقی میمانند.
- روشهای احیای مستقیم: در این روش، از گازهای احیا کننده مانند هیدروژن یا گاز طبیعی برای تبدیل سنگ آهن به آهن اسفنجی استفاده میشود. آهن اسفنجی، محصول میانی فرآیند احیای مستقیم است که به عنوان ماده اولیه در تولید فولاد در کورههای قوس الکتریکی استفاده میشود.
- روشهای فرآوری پلاسری: این روش از نوینترین روشهای فرآوری سنگ آهن است که از روشهای الکتروستاتیکی برای جداسازی ذرات سنگ آهن استفاده میکند. در این روش، ذرات سنگ آهن باردار شده و به الکترودهای مثبت و منفی هدایت میشوند. ذرات با بار مثبت به سمت الکترود منفی و ذرات با بار منفی به سمت الکترود مثبت جذب میشوند.
انتخاب روش مناسب فرآوری آهن، به عوامل مختلفی بستگی دارد و باید توسط متخصصان با در نظر گرفتن فاکتورهای مختلف انجام شود.
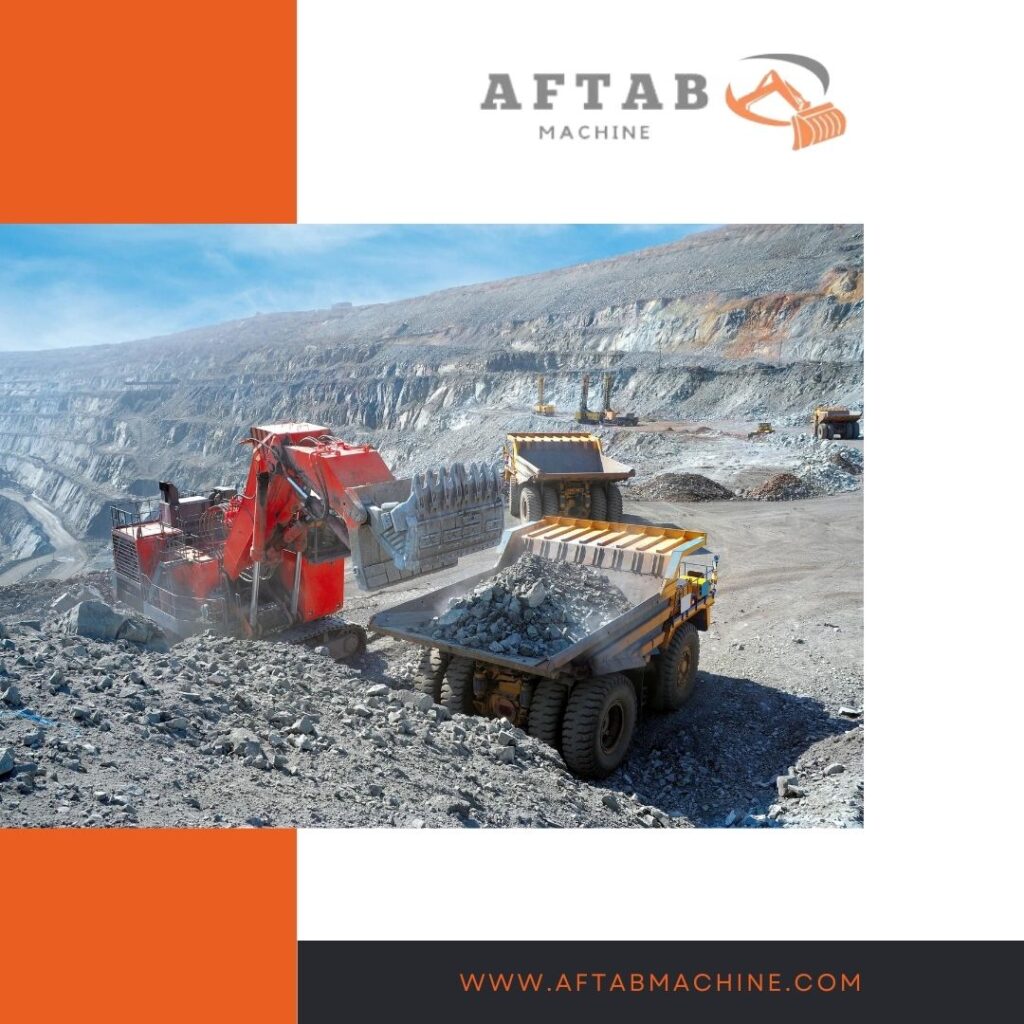
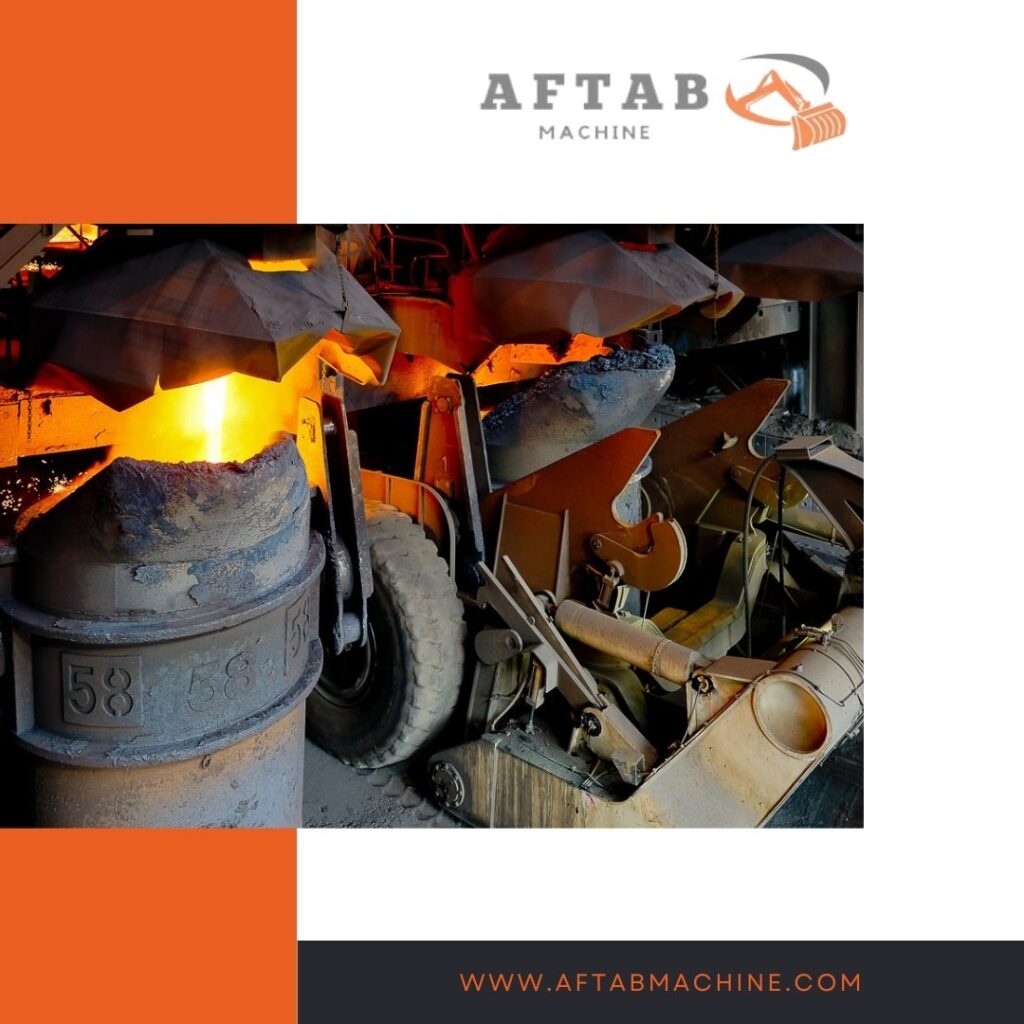
مراحل فرآوری سنگ آهن
فرآوری سنگ آهن، سفری پرمخاطره و چند مرحلهای است که طی آن، سنگ آهن با عیار پایین به فلز آهن خالص و قابل استفاده تبدیل میشود. این مراحل به طور کلی شامل موارد زیر است:
استخراج سنگ آهن
اولین مرحله از فرآیند فرآوری سنگ آهن، استخراج آن از معدن است. روشهای مختلفی برای استخراج سنگ آهن وجود دارد که از جمله آنها میتوان به استخراج روباز، استخراج زیرزمینی و حفاری هیدرولیکی اشاره کرد.
خردایش و آسیاب
پس از استخراج، سنگ آهن به قطعات کوچکتر خرد شده و آسیاب میشود. این امر به منظور آزادسازی ذرات کانیهای آهن از سنگ مادر و افزایش سطح تماس آنها با مواد شیمیایی در مراحل بعدی فرآیند انجام میشود.
غنیسازی
در مرحله غنیسازی، از روشهای مختلفی مانند جداسازی مغناطیسی، ثقلی یا flotation برای جداسازی کانیهای آهن از ناخالصیها استفاده میشود. انتخاب روش مناسب غنیسازی به نوع سنگ آهن و ناخالصیهای موجود در آن بستگی دارد.
پیشگرمایش
- در مرحله پیشگرمایش، سنگ آهن غنی شده تا دمای بالایی (حدود 700 تا 800 درجه سانتیگراد) گرم میشود. این امر به منظور آماده سازی سنگ آهن برای مرحله احیاء انجام میشود.
احیاء
در مرحله احیاء، اکسیژن از سنگ آهن جدا شده و فلز آهن خالص به دست میآید. برای احیای سنگ آهن از روشهای مختلفی مانند احیای مستقیم، احیای در کوره بلند و احیای در کوره دوار استفاده میشود.
تصفیه
پس از احیاء، آهن خام به دست آمده ممکن است حاوی ناخالصیهایی مانند گوگرد، فسفر و سیلیسیم باشد. در مرحله تصفیه، این ناخالصیها از آهن جدا شده و فلز آهن خالص و قابل استفاده به دست میآید.
ریختهگری
در نهایت، آهن خالص در قالبهای مختلف ریخته شده و محصولات نهایی مانند میلگرد، تیرآهن و ورق فولاد تولید میشود.
مراحل فرآوری سنگ آهن، فرآیندی پیچیده و تخصصی است که نیازمند دانش و تجربه کافی در این زمینه است. با درک عمیق این مراحل، میتوان به نقش بیبدیل فرآوری سنگ آهن در تولید فولاد و توسعه صنایع مختلف پی برد.
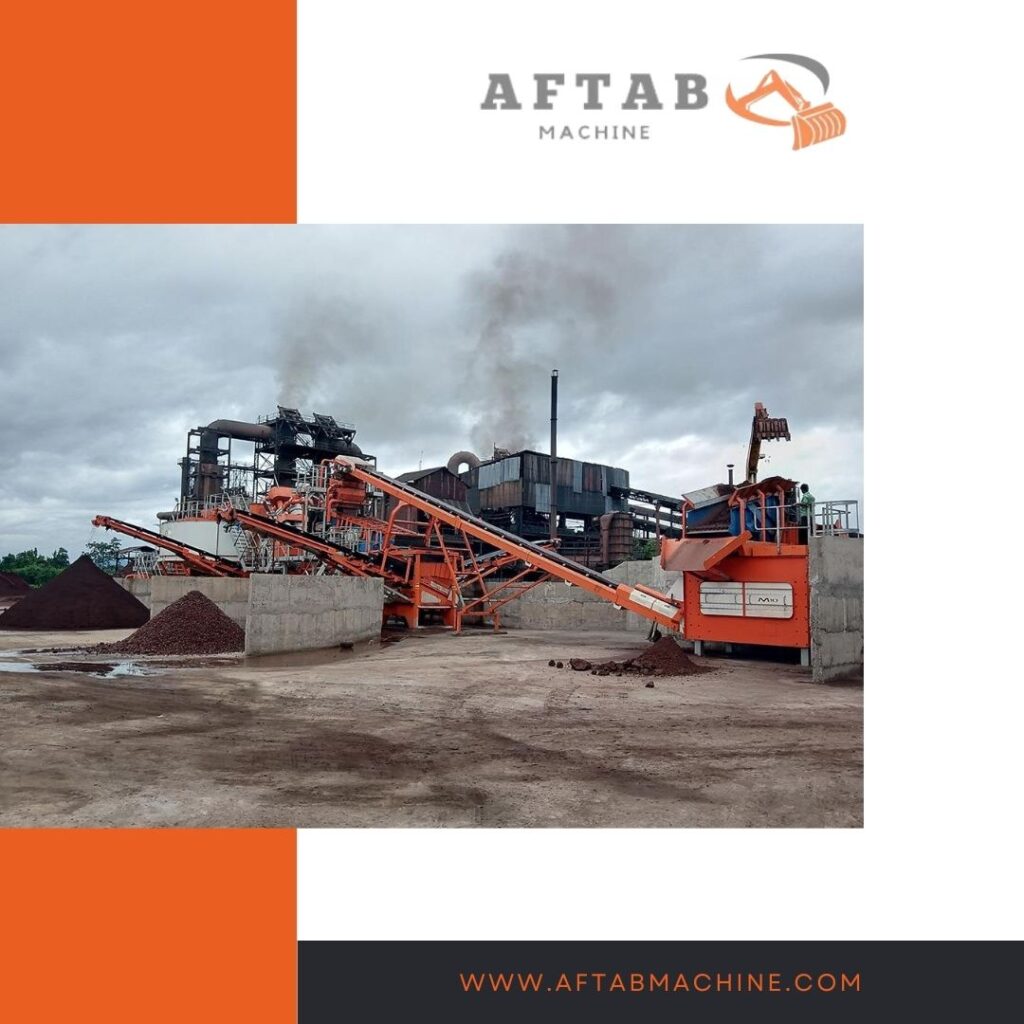
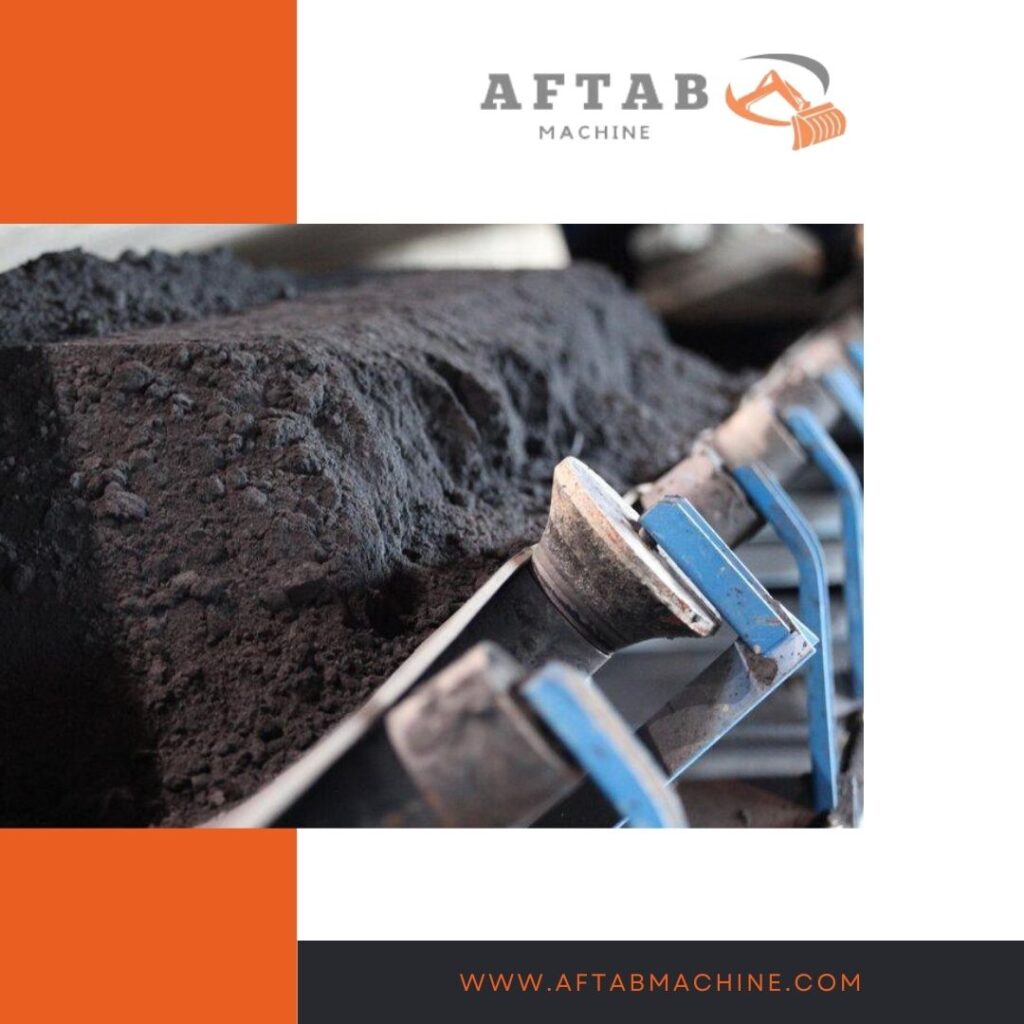
فرآوری سنگ آهن مگنتیت
سنگ آهن مگنتیت به دلیل دارا بودن خاصیت مغناطیسی، از جمله سنگ آهنهایی است که به طور خاص با استفاده از روشهای جداسازی مغناطیسی فرآوری میشود. در این روش، از نیروی مغناطیس برای جداسازی ذرات کانیهای آهن (مگنتیت) از ناخالصیها استفاده میشود.
مراحل فرآوری سنگ آهن مگنتیت به طور کلی شامل موارد زیر است:
خردایش و آسیاب
در اولین مرحله، سنگ آهن مگنتیت به قطعات کوچکتر خرد شده و آسیاب میشود. این امر به منظور آزادسازی ذرات کانیهای مگنتیت از سنگ مادر و افزایش سطح تماس آنها با میدان مغناطیسی در مراحل بعدی فرآیند انجام میشود.
جداسازی مغناطیسی
در مرحله جداسازی مغناطیسی، سنگ آهن خرد شده و آسیاب شده از میان یک نوار نقاله عبور میکند که در زیر آن آهنرباهای قدرتمندی قرار گرفتهاند. ذرات کانیهای مگنتیت به دلیل خاصیت مغناطیسی خود به آهنرباها جذب شده و از ناخالصیها جدا میشوند.
آسیاب مجدد
پس از جداسازی مغناطیسی اولیه، ذرات کانیهای مگنتیت که ممکن است هنوز به ناخالصیها آغشته باشند، مجدداً آسیاب میشوند تا ذرات ناخالصی از آنها جدا شود.
جداسازی مغناطیسی نهایی
پس از آسیاب مجدد، ذرات کانیهای مگنتیت در معرض جداسازی مغناطیسی نهایی قرار میگیرند. در این مرحله، از آهنرباهای قویتر و روشهای پیشرفتهتر جداسازی مغناطیسی استفاده میشود تا ناخالصیهای باقیمانده نیز از ذرات کانیهای مگنتیت جدا شوند.
تغلیظ
در نهایت، ذرات کانیهای مگنتیت جدا شده تغلیظ شده و به صورت کنسانتره سنگ آهن مگنتیت با عیار بالا در میآیند. این کنسانتره میتواند به عنوان ماده اولیه در تولید فولاد در کورههای بلند یا کورههای قوس الکتریکی استفاده شود.
فرآوری سنگ آهن مگنتیت به دلیل سادگی و کارایی بالا، یکی از روشهای متداول فرآوری سنگ آهن است. این روش به ویژه برای سنگ آهنهایی که عیار بالایی از مگنتیت دارند، بسیار مناسب است.
جزئیات کامل درباره قیمت دستگاه الکترووینینگ را اینجا بخوانید.
فرآوری آهن پلاسری
فرآوری آهن پلاسری، نوینترین روش فرآوری سنگ آهن است که برای استخراج ذرات ریز کانیهای آهن از معادن پلاسری به کار میرود. این روش از نیروی الکترواستاتیک برای جداسازی ذرات کانیهای آهن از ناخالصیها استفاده میکند.
مراحل فرآوری آهن پلاسری به طور کلی شامل موارد زیر است:
- آمادهسازی
در مرحله آمادهسازی، سنگ آهن پلاسری خرد شده و آسیاب میشود تا ذرات آن به اندازه مناسب برای فرآیند جداسازی الکترواستاتیک درآیند.
- جداسازی الکترواستاتیک
در مرحله جداسازی الکترواستاتیک، ذرات سنگ آهن پلاسری باردار شده و در معرض میدان الکتریکی قرار میگیرند. ذرات کانیهای آهن به دلیل بار الکتریکی خود به الکترودهای مثبت جذب شده و از ناخالصیها که بار الکتریکی ندارند یا بار منفی دارند، جدا میشوند.
- تغلیظ
در نهایت، ذرات کانیهای آهن جدا شده تغلیظ شده و به صورت کنسانتره سنگ آهن پلاسری با عیار بالا در میآیند. این کنسانتره میتواند به عنوان ماده اولیه در تولید فولاد در کورههای بلند یا کورههای قوس الکتریکی استفاده شود.
فرآوری آهن پلاسری مزایای قابل توجهی نسبت به روشهای سنتی فرآوری سنگ آهن دارد. این روش میتواند ذرات ریز کانیهای آهن را که در روشهای سنتی قابل استخراج نیستند، استخراج کند و عیار سنگ آهن را به طور قابلتوجهی افزایش دهد.
علاوه بر این، فرآوری آهن پلاسری به مصرف آب و انرژی کمتری نیاز دارد و آلایندگی زیستمحیطی کمتری ایجاد میکند. به همین دلیل، این روش به عنوان روشی نوین و پایدار برای فرآوری سنگ آهن در حال توسعه و گسترش است.
جمعبندی
فرآوری سنگ آهن، سفری پیچیده و چند مرحلهای است که طی آن، سنگ آهن با عیار پایین به فلز آهن خالص و قابل استفاده تبدیل میشود. این فرآیند شامل مراحل مختلفی از جمله خردایش، آسیاب، جداسازی، تغلیظ و در نهایت تصفیه میشود.
روشهای مختلفی برای فرآوری سنگ آهن وجود دارد که هر کدام مزایا و معایب خاص خود را دارند. انتخاب روش مناسب فرآوری سنگ آهن به عهدهی متخصصان و با در نظر گرفتن فاکتورهای مختلف مانند نوع سنگ آهن، ناخالصیهای موجود در آن، ظرفیت کارخانه فرآوری و مسائل اقتصادی انجام میشود.
هدف نهایی فرآوری سنگ آهن، به دست آوردن کنسانتره سنگ آهن با عیار بالا است که به عنوان ماده اولیه در تولید فولاد در کورههای بلند یا کورههای قوس الکتریکی استفاده میشود.
فرآوری سنگ آهن نقش حیاتی در صنعت فولاد ایفا میکند و بدون این فرآیند، تولید فولاد مدرن و بسیاری از محصولات و سازههای فلزی که در زندگی روزمره ما به کار میروند، غیرممکن خواهد بود.
دانش و درک عمیق از فرآوری سنگ آهن، برای مهندسین معدن، متالورژیستها و متخصصان صنایع فولاد ضروری است.
مراحل فرآوری سنگ آهن به طور کلی شامل خردایش، آسیاب، جداسازی، تغلیظ و تصفیه میشود. در هر مرحله از این فرآیند، ناخالصیها از کانیهای آهن جدا شده و عیار کنسانتره نهایی افزایش مییابد.
هدف نهایی فرآوری سنگ آهن، به دست آوردن کنسانتره سنگ آهن با عیار بالا است که به عنوان ماده اولیه در تولید فولاد در کورههای بلند یا کورههای قوس الکتریکی استفاده میشود.
نوع سنگ آهن، ناخالصیهای موجود در آن، ظرفیت کارخانه فرآوری، مسائل اقتصادی و الزامات زیستمحیطی از جمله عواملی هستند که در انتخاب روش مناسب فرآوری سنگ آهن نقش دارند.