توضیحات
مشخصات فنی دستگاه سرند دوار
دستگاه سرند دوار برای جداسازی، طبقهبندی و حذف ناخالصیها از مواد خام به کار میرود. طراحی این دستگاه به گونهای است که بتواند در شرایط سخت معادن مثل رطوبت بالا، سایش شدید و بار سنگین، عملکرد پایدار و قابل اعتماد داشته باشد. در ادامه با مشخصات فنی مهم این دستگاه آشنا میشویم.
- سرند دوار بین ۱۰۰۰ تا ۳۰۰۰ میلیمتر قطر و تا ۸ متر طول دارد. هر چه قطر و طول بیشتر باشد، ظرفیت و کیفیت تفکیک نیز افزایش مییابد.
- جنس بدنه اغلب از فولاد سختکاریشده یا فولاد ضد سایش ساخته میشود تا مقاومت بالایی در برابر خوردگی و سایش ذرات معدنی داشته باشد. مشها، بسته به نوع ماده معدنی، از فولاد کربنی، فولاد ضدزنگ یا پلیاورتان ساخته میشوند.
- توریها به صورت قابل تعویض طراحی میشوند و میتوانند از نوع پانچ شده، مشبندی جوشی یا مش بافته باشند. اندازه سوراخ مش بین ۵ تا ۱۰۰ میلیمتر است.
- سرند دوار با الکتروموتور سهفاز صنعتی و گیربکس کوپل مستقیم یا زنجیری کار میکند. قدرت الکتروموتور متناسب با طول و قطر درام، بین 5.5 تا 30 کیلووات در نظر گرفته میشود.
- سرعت چرخش بین ۱۰ تا ۳۰ دور در دقیقه بسته به نوع مواد و قطر استوانه تنظیم میشود. سرعت بیش از حد موجب پرتاب مواد و کاهش دقت تفکیک میشود.
- استوانه با زاویه ۳ تا ۷ درجه نسبت به سطح افق نصب میشود تا مواد درون درام حرکت تدریجی و مارپیچی داشته باشند.
- بسته به طراحی، ظرفیت سرند دوار میتواند از ۵۰ تا بیش از ۵۰۰ تن در ساعت متغیر باشد.
- در کاربردهای خاص مانند معادن زغالسنگ یا مواد ریزدانه، سیستم اسپری آب یا پوشش غبارگیر برای کنترل محیطی در نظر گرفته میشود.
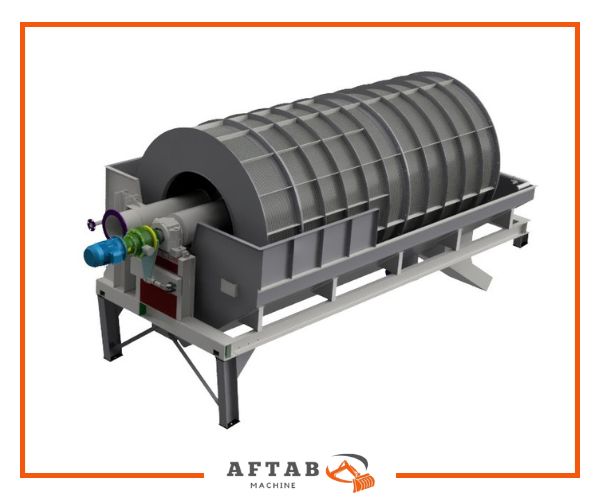
آشنایی با عملکرد سرند دوار در فرآیند جداسازی
سرند دوار با بهرهگیری از حرکت چرخشی مداوم، ذرات ورودی را بر اساس اندازه، وزن و شکل آنها تفکیک میکند.
مواد معدنی پس از ورود به داخل استوانه چرخان، تحت تأثیر نیروی گریز از مرکز و اصطکاک داخلی، شروع به حرکت در امتداد سطح توری میکنند.
ذرات ریزتر از اندازه مش از سوراخها عبور کرده و به عنوان ماده زیرسرند جمعآوری میشوند. ذرات درشتتر در مسیر استوانه حرکت کرده و از انتهای دیگر تخلیه میشوند.
این عملکرد مداوم باعث افزایش بهرهوری و کاهش توقف در خطوط تولید معدنی میشود. در ادامه با جزییات بیشتری به عملکرد سرند چرخشی میپردازیم.
مکانیزم چرخشی سرند و تفکیک مواد
مکانیزم اصلی سرند دوار مبتنی بر چرخش استوانهای مشبک است که توسط الکتروموتور و سیستم انتقال قدرت به حرکت درمیآید.
زاویه شیب دار استوانه و حرکت چرخشی باعث میشود مواد به صورت مارپیچی به جلو رانده شوند. بسته به طراحی دستگاه، ممکن است استوانه دارای بخشهای چندمرحلهای با مشهایی با اندازههای متفاوت باشد تا فرآیند تفکیک چندگانه انجام شود. این مکانیزم به ویژه برای مواد معدنی مرطوب، چسبنده یا دارای تودههای غیرهمگن بسیار مؤثر است، چرا که از گرفتگی توری جلوگیری میکند و تفکیک پیوسته را ممکن میکند.
نحوه تغذیه ورودی و خروجی مواد
در سیستمهای معدنی، تغذیه ورودی به سرند دوار از طریق نوار نقاله یا هاپر انجام میشود. مواد خام پس از ورود، به طور یکنواخت در داخل استوانه توزیع شده و فرآیند جداسازی آغاز میشود.
خروجی دستگاه نیز شامل دو بخش اصلی است:
- مواد ریز، خروجی از سوراخهای مش، که به عنوان محصول زیرسرند شناخته میشوند.
- مواد درشت که از انتهای استوانه خارج میشوند.
طراحی بهینه ورودی و خروجی نقش مهمی در جلوگیری از گرفتگی، حفظ سرعت خط تولید و افزایش راندمان دارد.
تنظیم سرعت چرخش و قطر مش
دو پارامتر کلیدی در بهینهسازی عملکرد سرند دوار، سرعت چرخش استوانه و اندازه مش (قطر سوراخهای توری) هستند.
سرعت چرخش باید به گونهای تنظیم شود که مواد فرصت کافی برای تماس با سطح مش و جداسازی را داشته باشند، بدون آن که باعث پاشیدن یا تجمع غیرطبیعی شوند. این سرعت بین 10 تا 30 دور در دقیقه بسته به قطر استوانه و نوع ماده تنظیم میشود. قطر مش نیز بر اساس نیاز عملیاتی تعیین میشود و بین 5 میلیمتر تا 100 میلیمتر متغیر است. مشهای قابل تعویض امکان انعطافپذیری بالا در خطوط تولید معدنی را فراهم میکنند.
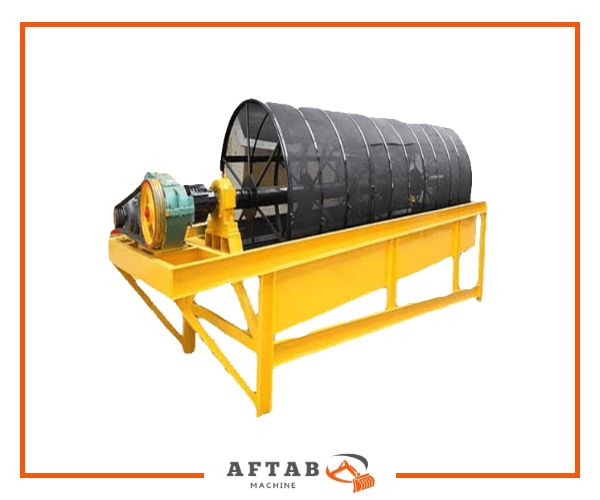
انواع سرند دوار بر اساس کاربرد و طراحی
با توجه به نوع ماده معدنی، میزان رطوبت، ظرفیت مورد انتظار و ویژگیهای فیزیکی خوراک ورودی، طراحیهای مختلفی از سرند دوار مورد استفاده قرار میگیرد. در این میان، چهار نوع اصلی از سرند دوار بر اساس کاربرد و طراحی در معادن شناخته شدهاند که با آنها آشنا میشویم.
سرند دوار صنعتی سنگین
این نوع سرند دوار برای کار در شرایط سخت معادن سنگین طراحی شده است و عمدتا در فرآیندهای اولیه جداسازی مواد درشت و سنگین مانند سنگآهن، مس، بوکسیت و منگنز کاربرد دارد.
با داشتن استوانهای با قطر زیاد، بدنهای تقویتشده از فولاد ضدسایش و موتورهایی با توان بالا، توانایی پردازش حجم بالایی از خوراک ورودی را دارد.
طراحی مش چندمرحلهای در داخل درام به تفکیک دقیقتر مواد در سایزهای مختلف کمک میکند و ساختار مقاوم آن، عمر کاری بالا و حداقل توقفات در خطوط تولید را تضمین میکند.
سرند دوار سبک برای مواد نرم
این دستگاه برای معادنی که با مواد کمسخت یا ریزدانه سر و کار دارند، مانند زغالسنگ، خاک فسفات، نمک یا تالک، استفاده میشود. این دستگاه وزن و مصرف انرژی کمتری دارد و از نظر اقتصادی مقرون به صرفه است. به دلیل داشتن استوانههای نازکتر و موتورهای کوچکتر، نگهداری و جابجایی این سرند آسانتر است. طراحی ساده آن موجب میشود که برای واحدهای با ظرفیت متوسط یا معادن با منابع محدود بسیار مناسب باشد.
سرند روتاری با سیستم پاشش آب
برای شستوشو و تفکیک همزمان مواد، این سرند به نازلهای آبپاش تجهیز شده که با پاشیدن آب فشار بالا به سطح مش و ذرات ورودی، خاک، گل و رسهای چسبیده به سنگها را جدا میکند. این سیستم برای معادنی که خوراک ورودی مرطوب، چسبنده یا دارای آلودگی سطحی زیاد است، مانند زغالسنگ یا سنگآهن شستنی، بسیار مفید است. استفاده از این مدل، علاوه بر افزایش دقت جداسازی، باعث کاهش بار وارد بر تجهیزات پاییندستی مانند سنگشکنها یا واحدهای پرعیارسازی میشود.
سرندهای افقی و شیبدار
سرند افقی و شیبدار بر اساس زاویه نصب در خطوط فرآوری دستهبندی میشوند.
سرند شیبدار با زاویه ۳ تا ۷ درجه نصب میشود تا حرکت طبیعی مواد از ورودی به سمت خروجی آسان شود. این نوع طراحی برای موادی با دانهبندی درشت و جریان یکنواخت مناسب است.
سرند افقی بیشتر در فرآیندهایی استفاده میشود که نیاز به کنترل دقیق زمان ماندن ذرات در درام دارند، مانند فرآوری مواد ریزدانه یا دارای چسبندگی بالا. انتخاب بین این دو نوع طراحی به نوع فرآیند، ویژگیهای فیزیکی ماده و ساختار کلی خط تولید بستگی دارد.
کاربرد دستگاه سرند دوار (گردان) در صنایع معدنی
دستگاه سرند دوار به واسطه طراحی چرخشی و استفاده از مشهای متنوع، مواد را بر اساس اندازه ذرات در مقیاس صنعتی طبقهبندی میکند که در صنایع وابسته به معدن مانند بازیافت، صنایع شیمیایی و پالایش مواد به طور گسترده استفاده میشود. در ادامه با کاربردهای سرند چرخشی بیشتر آشنا میشویم.
جداسازی سنگ دانهها در معادن
یکی از اصلیترین کاربردهای سرند دوار، تفکیک سنگدانهها و کانیهای معدنی بر اساس اندازه ذرات در مرحله اولیه فرآوری است. پس از استخراج ماده خام از معدن، مواد وارد دستگاه سرند دوار میشوند تا ذرات درشت از ریز جدا شوند. این عملیات نه تنها باعث کاهش فشار وارد بر سنگشکنهای ثانویه و دستگاههای خردایش میشود، بلکه راندمان کلی کارخانه را نیز افزایش میدهد. در معادن سنگآهن، مس، سرب و روی، استفاده از سرند دوار قبل از مرحله خردایش، از هدررفت انرژی و استهلاک تجهیزات جلوگیری میکند.
الککردن کودهای شیمیایی یا آلی
در صنایع تولید کود، بهویژه کودهای آلی یا گرانولهشده، نیاز به طبقهبندی دقیق ذرات وجود دارد. سرند چرخشی در این حوزه برای جدا کردن ذرات بیش از حد درشت یا ریز و یکنواختسازی اندازه دانهها استفاده میشود. استفاده از این دستگاه در واحدهای فرآوری کود فسفاته، اوره یا کمپوست آلی باعث بهبود کیفیت محصول نهایی میشود که میتواند رضایت خریداران بیشتری را جلب کند.
همچنین، سرند دوار مانع از ورود ذرات نامطلوب به کیسهزن یا واحدهای بستهبندی میشود که در کنترل کیفیت بسیار مهم است.
تفکیک ضایعات در خط بازیافت
در خطوط بازیافت صنعتی، به ویژه بازیافت پسماندهای معدنی یا ساختمانی، سرند دوار برای جداسازی مکانیکی اجزای قابل تفکیک مانند سنگ، پلاستیک، فلزات و مواد سبک استفاده میشود. ساختار چرخشی سرند موجب میشود مواد به خوبی در طول درام غربال شده و بسته به اندازه از یکدیگر جدا شوند. در خطوط بازیافت معادن متروکه یا پسماند حاصل از استخراج، استفاده از سرند دوار باعث کاهش ضایعات و بازیابی بخشی از مواد ارزشمند میشود که از نظر اقتصادی قابل توجه است.
جداسازی ذرات چوب و خاک اره
در برخی صنایع معدنی مانند تولید بریکت از زغالسنگ یا پالایش تالک و بنتونیت، وجود ناخالصیهایی مانند چوب، الیاف یا خاکاره کیفیت محصول نهایی را کاهش میدهد. سرند دوار در این موارد برای حذف ناخالصیهای آلی و سبک از جریان مواد معدنی به کار میرود. با توجه به حرکت چرخشی یکنواخت و توانایی غربالگری پیوسته، دستگاه میتواند ذرات ریز یا سبکتر را از جریان ماده اصلی جدا کرده و موجب افزایش خلوص مواد شود. در صنایعی که از مواد معدنی برای پرکنندههای صنعتی، مواد ساینده یا نسوز استفاده میشود، جداسازی این نوع ذرات اهمیت دو چندان دارد.
جمع بندی
در صنعت معدن، استفاده از تجهیزات مطمئن و بادوام مانند سرند دوار، تضمینی برای کاهش هزینهها و افزایش بازدهی است. همانطور که در این مقاله بررسی شد، سرند چرخشی نقش کلیدی در دانهبندی دقیق و جداسازی مواد دارد. اگر در فکر خرید سرند دوار هستید، فراموش نکنید که کیفیت ساخت، مشخصات فنی و خدمات پس از فروش، مهمتر از تنها توجه به قیمت سرند دوار هستند. انتخاب درست شما، گامی مؤثر در توسعه و رشد پایدار مجموعهتان خواهد بود.
نقد و بررسیها
هنوز بررسیای ثبت نشده است.