Iron processing: a journey from the heart of the stone to the pinnacle of industry
Iron processing is an amazing and complex journey that extracts the precious metal of iron from the heart of lifeless stones and gives it to the heart of industry and civilization. This process is a testimony to human creativity and innovation in taming nature and creating amazing achievements. In this article, we will learn about the amazing stages of iron ore processing, its new and traditional methods and the irreplaceable role of iron in various industries.
In today’s world, steel, as an alloy of iron, forms the backbone of many structures and machines. From soaring skyscrapers to modern and elegant cars, traces of iron are evident in the fabric of human life. Iron processing is the key to obtaining this precious and vital metal.
In this article, we discuss the key concepts of iron ore processing, the various stages of this process, and the countless uses of iron in various industries in a simple and eloquent language.
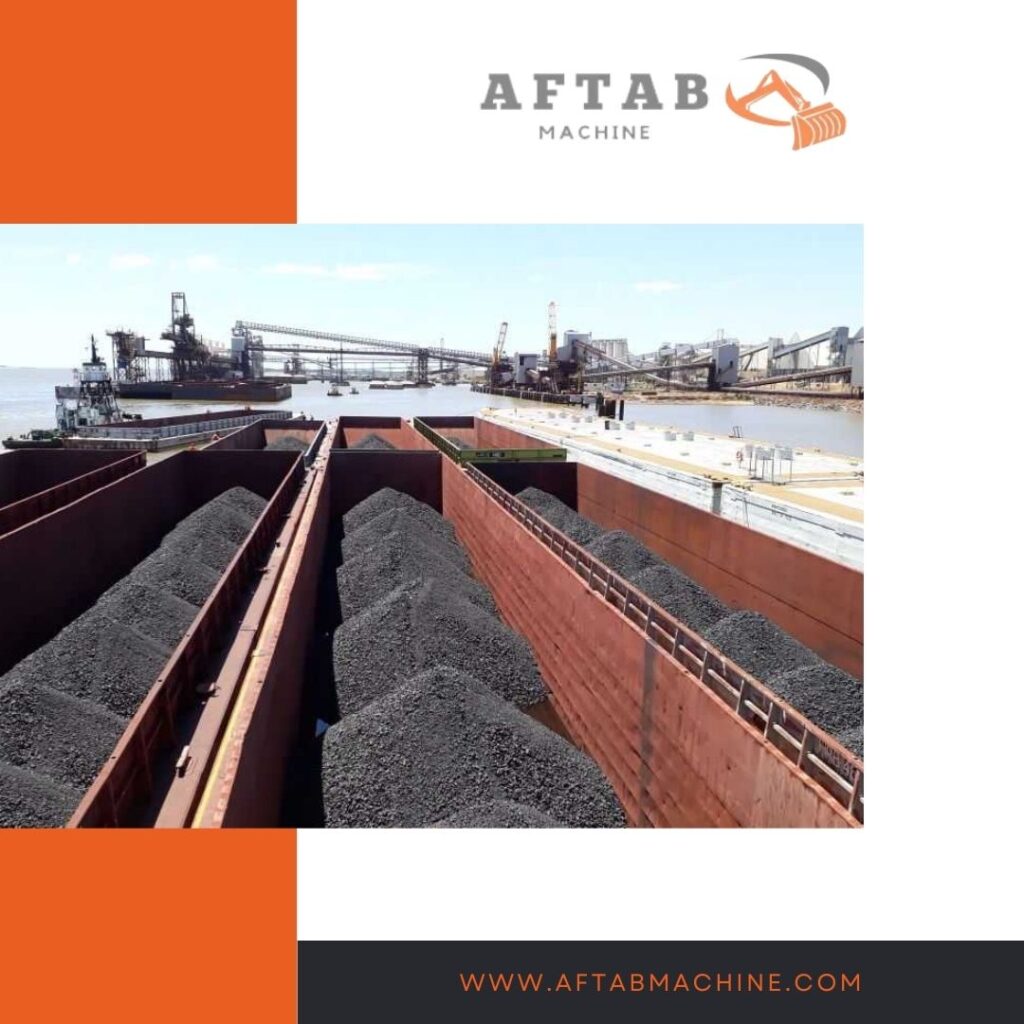
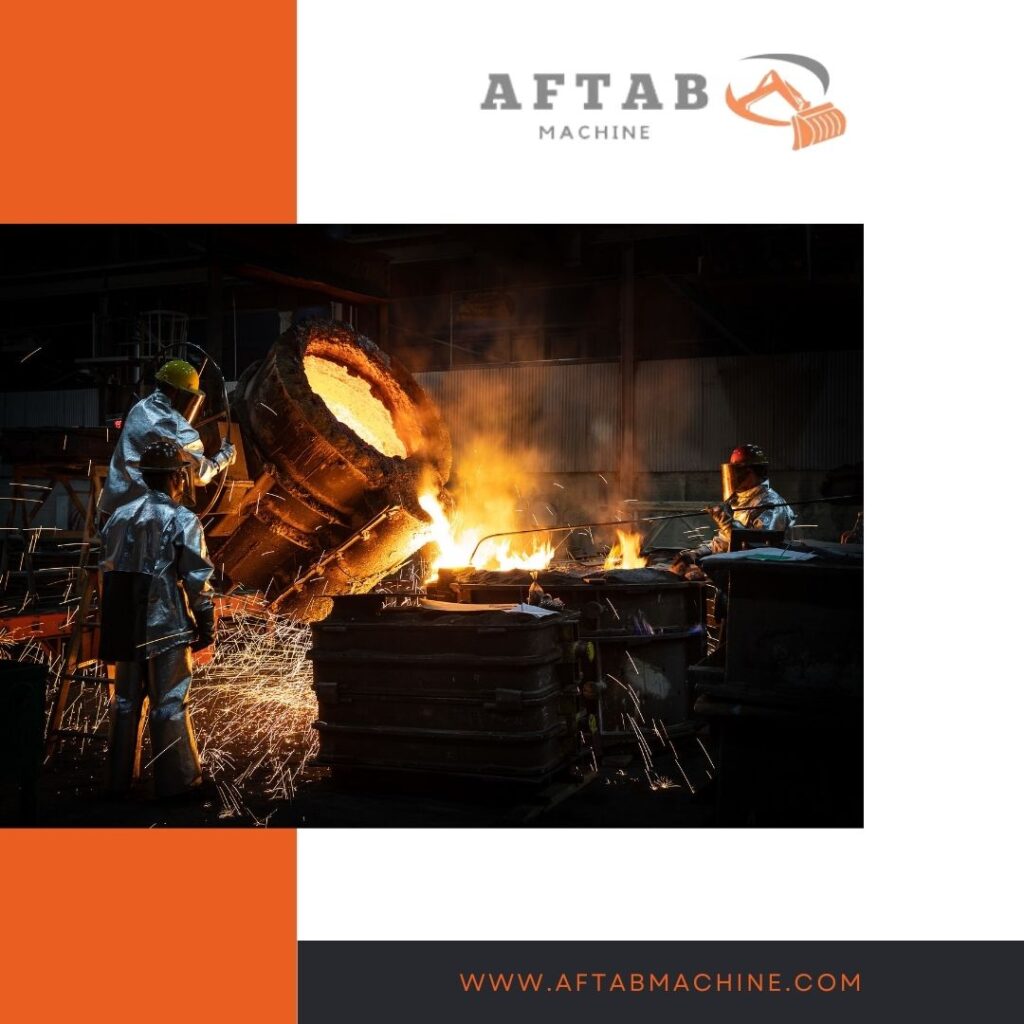
What is iron processing?
Iron processing is a multi-step and complex process during which low-grade iron ore is transformed into pure and usable iron metal. This process includes various stages including iron ore extraction, crushing and grinding, separation of impurities and reduction of iron ore to iron metal.
In nature, iron ore is found mixed with other minerals. The purpose of iron ore processing is to separate this valuable metal from impurities and increase its grade. The iron ore processing process plays a key role in the production of steel, which is used as one of the most important metal alloys in various industries, including construction, automobiles, household appliances, and heavy industries.
Iron ore processing steps depend on the type of iron ore, the impurities in it and the technologies used in the processing factories. However, in general, this process can be divided into the stages of crushing and grinding, enrichment, preheating and regeneration.
In the crushing and grinding stage, iron ore is turned into smaller pieces. Then, in the enrichment stage, various methods such as magnetic separation, gravity or flotation are used to separate iron minerals from impurities. In the preheating stage, the enriched iron ore is heated to a high temperature and finally, in the reduction stage, oxygen is separated from the iron ore and pure iron metal is obtained.
Iron processing is a necessary and vital process for the production of steel and the development of various industries. By deeply understanding this process and its different stages, one can realize its irreplaceable role in the modern world and human life.
Iron processing methods
Iron ore processing is a diverse path with different methods, each of which has its own advantages and disadvantages. Choosing the right processing method depends on factors such as the type of iron ore, the impurities in it, the capacity of the processing plant, and economic issues. In the following, we will introduce some common methods of iron processing:
Magnetic methods: This method uses the magnetic properties of some iron minerals such as magnetite to separate them from impurities. In this method, the crushed iron ore is passed through a magnetic field and the iron minerals are attracted due to their magnetic properties and separated from the impurities.
Gravitational methods: In this method, the difference in specific weight of iron minerals and impurities is used to separate them. Crushed iron ore is poured into a mixture of water and chemicals, and particles with a higher specific gravity (iron ores) settle to the bottom of the tank, and particles with a lower specific gravity (impurities) float on top of the tank.
Flotation methods: This method uses air bubbles to separate iron minerals from impurities. In this method, crushed iron ore is poured into a mixture of water and chemicals, and air bubbles bind to the iron ore particles and drive them to the surface of the tank, while the impurities remain at the bottom of the tank.
Direct reduction methods: In this method, reducing gases such as hydrogen or natural gas are used to convert iron ore into sponge iron. Sponge iron is an intermediate product of the direct reduction process, which is used as a raw material in the production of steel in electric arc furnaces.
Placer processing methods: This method is one of the newest iron ore processing methods that uses electrostatic methods to separate iron ore particles. In this method, iron ore particles are charged and directed to the positive and negative electrodes. Positively charged particles are attracted to the negative electrode and negatively charged particles are attracted to the positive electrode.Choosing the right iron processing method depends on various factors and should be done by experts considering various factors.
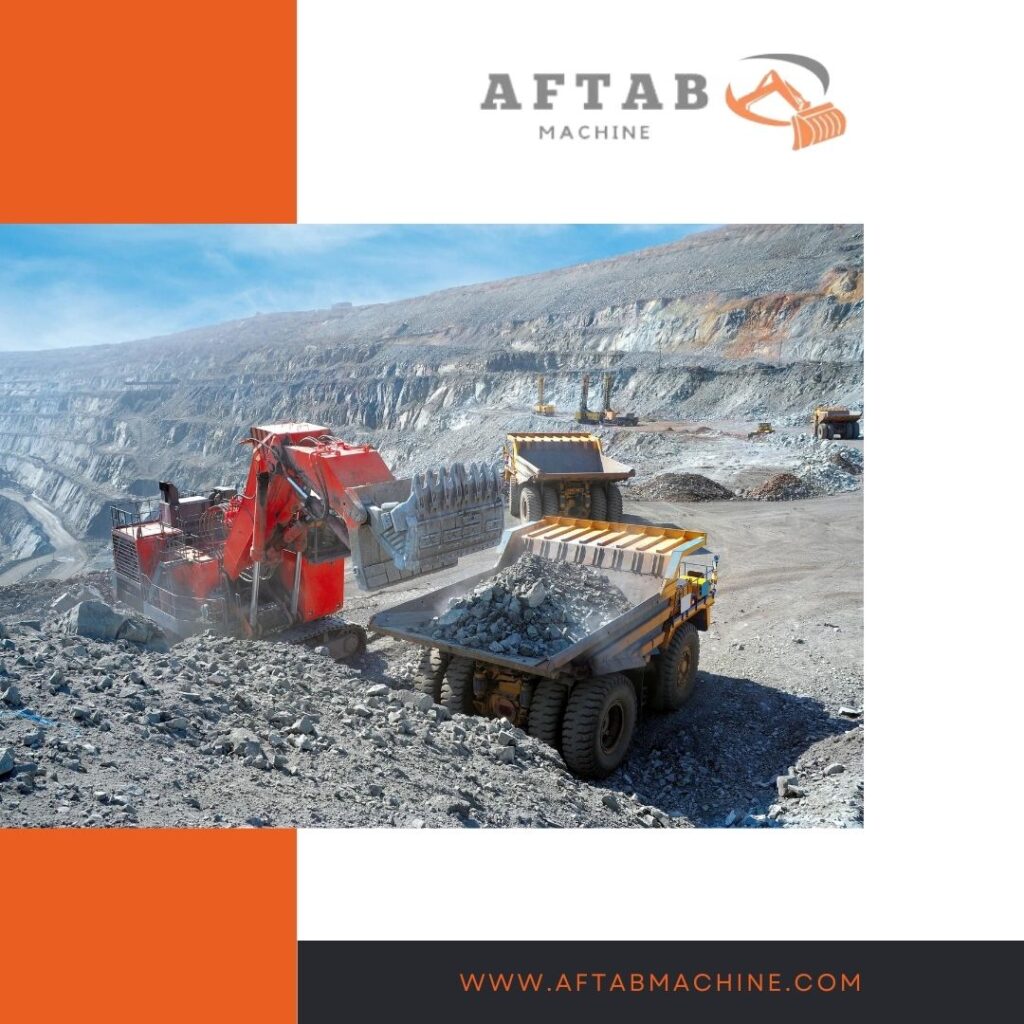
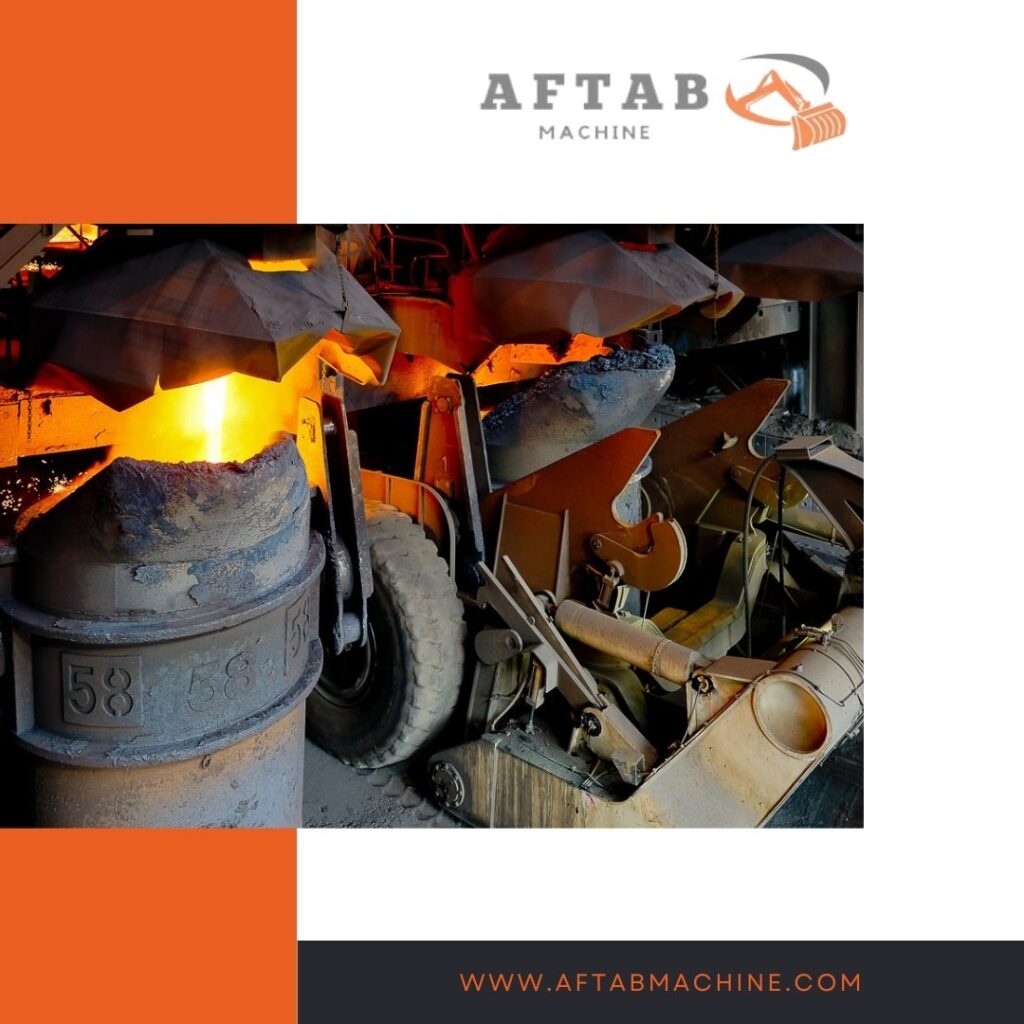
Iron ore processing steps
Iron ore processing is a risky and multi-step journey during which low-grade iron ore is transformed into pure and usable iron metal. These steps generally include the following:
Iron ore mining
The first step in the iron ore processing process is its extraction from the mine. There are various methods of iron ore extraction, among them open pit mining, underground mining and hydraulic drilling.
Crushing and grinding
After mining, iron ore is crushed into smaller pieces and ground. This is done in order to release the particles of iron minerals from the parent rock and increase their contact surface with chemicals in the next stages of the process.
Enrichment
In the enrichment stage, various methods such as magnetic separation, gravity or flotation are used to separate iron minerals from impurities. Choosing the right beneficiation method depends on the type of iron ore and the impurities in it.
preheating
In the preheating stage, enriched iron ore is heated to a high temperature (about 700 to 800 degrees Celsius). This is done in order to prepare the iron ore for the regeneration stage.
Revival
In the reduction stage, oxygen is separated from iron ore and pure iron metal is obtained. Various methods are used for iron ore recovery, such as direct recovery, blast furnace recovery, and rotary furnace recovery.
Purification
After reduction, the obtained pig iron may contain impurities such as sulfur, phosphorus and silicon. In the purification stage, these impurities are separated from iron and pure and usable iron metal is obtained.
Casting
Finally, pure iron is poured into various molds and final products such as rebar, beam and steel sheet are produced.
Iron ore processing is a complex and specialized process that requires sufficient knowledge and experience in this field. With a deep understanding of these stages, one can understand the irreplaceable role of iron ore processing in steel production and the development of various industries.
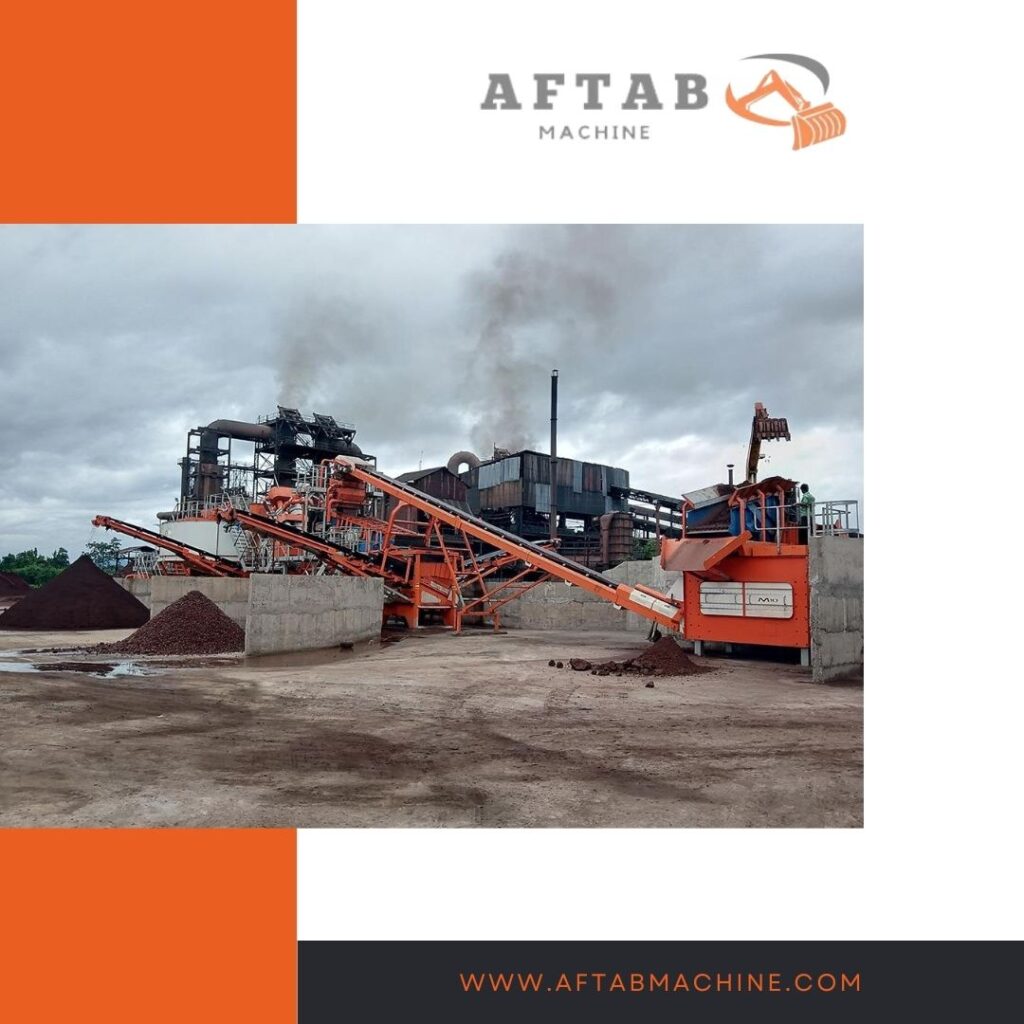
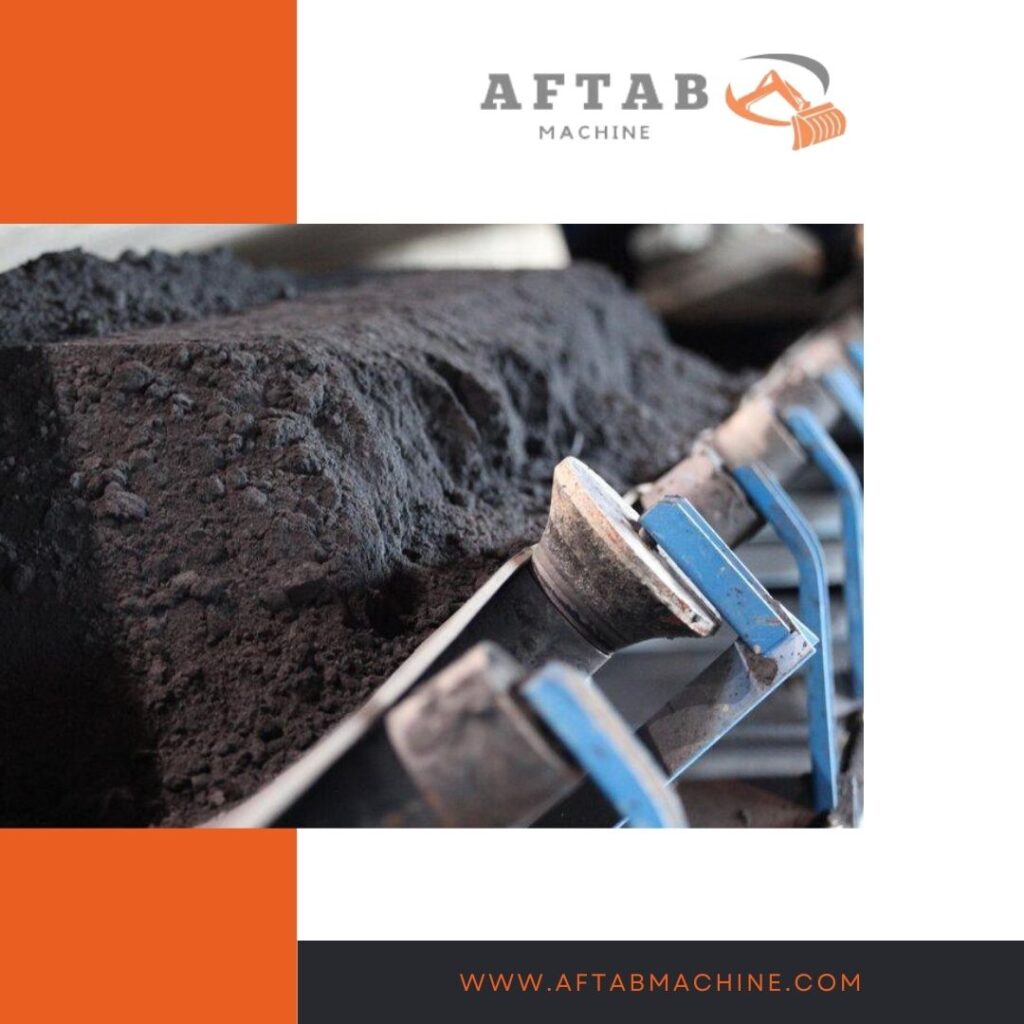
Magnetite iron ore processing
Due to its magnetic property, magnetite iron ore is one of the iron ores that is specifically processed using magnetic separation methods. In this method, magnetic force is used to separate particles of iron minerals (magnetite) from impurities.
The processing steps of magnetite iron ore generally include the following:
Crushing and grinding
In the first step, magnetite iron ore is crushed into smaller pieces and ground. This is done in order to release magnetite mineral particles from the parent rock and increase their contact surface with the magnetic field in the next stages of the process.
Magnetic separation
In the magnetic separation stage, the crushed and ground iron ore passes through a conveyor belt under which powerful magnets are placed. Magnetite mineral particles are attracted to magnets due to their magnetic properties and are separated from impurities.
Re-milling
After the initial magnetic separation, the magnetite mineral particles, which may still be impregnated with impurities, are ground again to remove the impurity particles.
Final magnetic separation
After re-grinding, magnetite mineral particles are subjected to final magnetic separation. At this stage, stronger magnets and more advanced magnetic separation methods are used to separate the remaining impurities from the magnetite mineral particles.
Condensation
Finally, the separated magnetite mineral particles are concentrated and become high grade magnetite iron ore concentrate. This concentrate can be used as a raw material in steel production in blast furnaces or electric arc furnaces.
Magnetite iron ore processing is one of the common methods of iron ore processing due to its simplicity and high efficiency. This method is especially suitable for iron ores that have a high grade of magnetite.
Placer iron processing
Placer iron processing is the newest method of iron ore processing, which is used to extract fine particles of iron minerals from placer mines. This method uses electrostatic force to separate iron mineral particles from impurities.
The processing steps of plasari iron generally include the following:
preparation
In the preparation stage, the placer iron ore is crushed and ground so that its particles are of the right size for the electrostatic separation process.
Electrostatic separation
In the electrostatic separation stage, placer iron ore particles are charged and exposed to an electric field. Iron mineral particles are attracted to positive electrodes due to their electrical charge and are separated from impurities that do not have an electrical charge or have a negative charge.
Condensation
Finally, the separated iron ore particles are concentrated and become a high grade placer iron ore concentrate. This concentrate can be used as a raw material in steel production in blast furnaces or electric arc furnaces.
Placer iron processing has significant advantages over traditional iron ore processing methods. This method can extract small particles of iron minerals that cannot be extracted in traditional methods and significantly increase the grade of iron ore.
In addition, the processing of plaser iron requires less water and energy consumption and creates less environmental pollution. For this reason, this method is being developed and expanded as a new and sustainable method for iron ore processing.
summary
Iron ore processing is a complex and multi-step journey through which low-grade iron ore is transformed into pure and usable iron metal. This process includes various stages including crushing, grinding, separation, concentration and finally purification.
There are different methods for processing iron ore, each of which has its own advantages and disadvantages. The selection of the appropriate method of iron ore processing is done by experts and taking into account various factors such as the type of iron ore, the impurities in it, the capacity of the processing plant and economic issues.
The ultimate goal of iron ore processing is to obtain high-grade iron ore concentrate, which is used as a raw material in the production of steel in blast furnaces or electric arc furnaces.
Iron ore processing plays a vital role in the steel industry, and without this process, the production of modern steel and many metal products and structures used in our daily lives would be impossible.
A deep knowledge and understanding of iron ore processing is essential for mining engineers, metallurgists and steel industry professionals.
Iron ore processing steps generally include crushing, grinding, separation, concentration and purification. At each stage of this process, impurities are separated from the iron minerals and the grade of the final concentrate increases.
The ultimate goal of iron ore processing is to obtain high-grade iron ore concentrate, which is used as a raw material in the production of steel in blast furnaces or electric arc furnaces.
The type of iron ore, the impurities in it, the capacity of the processing plant, economic issues and environmental requirements are among the factors that play a role in choosing the appropriate method of iron ore processing.